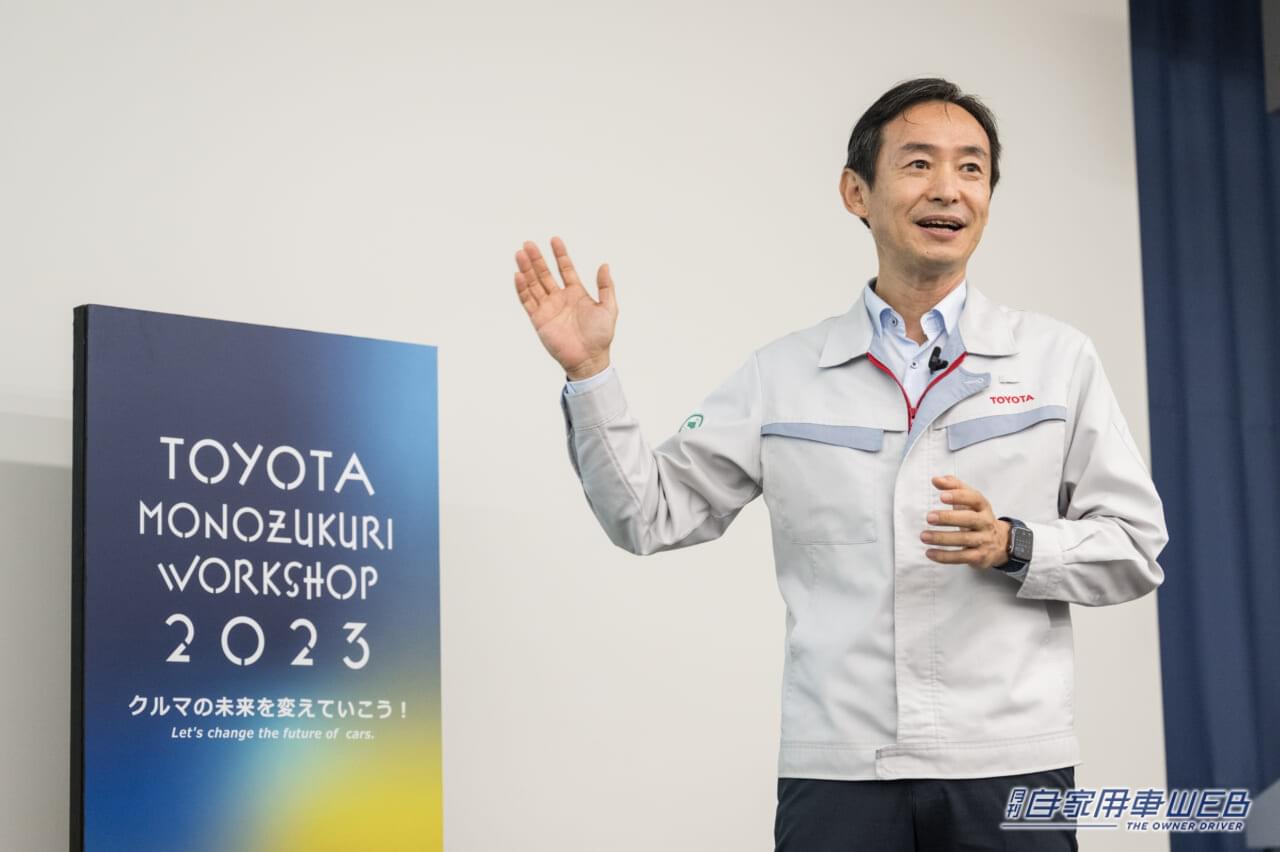
トヨタ自動車株式会社は、愛知県にある同社の貞宝工場、明知工場、元町工場で取り組まれている様々なモノづくり技術を「トヨタモノづくりワークショップ」としてメディアに公開した。そこには初公開となる、デジタルと革新技術でTPS(トヨタ生産方式)と現場力を進化させ、”もっといいクルマ”を生み出す新たな土壌が待っていた。
●文:月刊自家用車編集部
「技能/技術」と「デジタル・革新技術」の融合でモノづくりを進化させ、そしてリードタイムを短縮して、すばやく、何度も何度もチャレンジする!
ワークショップ冒頭で挨拶に立った執行役員Chief Production Officer(CPO)の新郷 和晃氏は、初代プリウスのHEVシステム開発、カローラ、プリウス、ヤリスなどの車両企画を担当するなど、開発畑を歩いてきた人物だ。ご本人は現職の内示を受けた時は正直、何かの間違いかと驚いたというが、「正解のない時代に開発と生産が垣根を越えてベンチャー企業のように一体となって未来を作ってほしい」という期待があったからだ」と語る。
また、豊田章男会長からは「働く人がイキイキともっと活躍できる工場にしてほしい」と言われ、そこから半年間に渡って世界中の現場を回り見えてきたことがあったという。それが「『誰かの仕事を楽にしたい』、『みんなの笑顔のために』という創業期から変わらぬ精神」、「モノづくりの『高い技能と技術』のしっかりとした継承」、「人財を鍛える現場の力」の3つだという。
トヨタが自ら開発して生産して生み出してきたハイブリッド用のモーター。
かつて豊田佐吉が自動織機を開発したように、今も無から有を生み出して、カイゼンを積み重ね魅力ある製品を世に出していく、スタートアップの力は健在である! とも語る。ハイブリッド用のモーターや電池、FCスタックやタンクなども外注委託に出すのではなく、自ら開発して生産して生み出してきたのもこの精神である。
さらに、現場で感じた3つのトヨタしか持ちえないモノづくりの強み、トヨタの「技」 をしっかり「継承」していくことこそがますます重要と語る。それは、2023年の今、これまでのエンジン車、HEVからPHEV、BEV、FCEVへと、自動車業界はゲームチェンジとも言える、生き残りを賭けた変革の時代を迎えているからだ。
この大変革を突き進むために、新郷 和晃CPOは「トヨタの技で、モノづくりの未来を変えたい」と言う。そのために、「技能/技術」と「デジタル・革新技術」の融合でモノづくりを進化させ、そしてリードタイムを短縮して「すばやく、何度も何度もチャレンジする」ことが必要と力説する。
例えば、ランドクルーザーに採用されているフレームの溶接では、熟練技能者は溶接する板と板の間の隙間に合わせて溶接棒の速度を細やかに調整することで高品質な溶接ができている。しかし、そのままロボットで自動化すると隙間がどうあろうと一定の動きしかできないため、隙間がアジャストできずに品質がバラついてしまう。人がどうやって隙間に合わせて調整するのか、ロボットに教えることで高い品質と生産性を両立する。その人の技能をさらに高めて、その高めた技能をさらにロボットに教えて高めていく。トヨタでは、このようなサイクルを回し続けて技能と技術を磨き続けている。
完成車生産を行う元町工場。
また、トヨタ生産方式(TPS)が根付き、全員がモノづくりへの情熱を持って、自らカイゼンを続けられる。そういった人を育てることもまさに現場の力であるという。完成車生産を行う元町工場ではここ1年間で4つの新作プロジェクトを立ち上げることができたといい、これはチームでのカイゼン活動、混流生産に対応した多能工化、さまざまな人作りを進めた現場の力でお客様の多様なニーズに応え、1000万台のフルラインナップを実現することができたと胸を張る。
デジタルの3D空間上でカイゼン活動。
トヨタのモノづくりスタートアップ拠点である貞宝工場では、設備の開発にあたり技能を持ったメンバーが、デジタルの3D空間上でカイゼン活動を重ね、それをリアルの設備生産に反映する仕組みがすでに動いている。また、全固体電池生産ラインでは技能者の創意工夫により、高速かつ高精度の生産が出来るようになってきているという。
こうした技能・技術のデジタルや革新技術の融合に加え、トヨタにはトヨタ生産方式(TPS)を基軸としたリードタイム短縮という技がある。以前は3年以上かかっていたクルマ開発ではあるが、「GRヤリス」や「水素エンジンカローラ」のように、レースの現場に開発やモノづくりの全員が集まり、走っては壊し、また走っては壊し、カイゼンしていくというサイクルを繰り返し、繰り返し、クイックに何度も回すことで、よりスピーディに新しいクルマをカタチにできるようになってきたとのこと。
明知工場のギガキャスト試作用設備。
リードタイム短縮と言えばもう一つ、今回初公開された明知工場のギガキャスト試作用設備だ。ギガキャストは、定期的な鋳造の型の交換が必要で、通常その交換に24 時間程度かかるという。トヨタでは、すでに創業から現在に至るまでエンジン製造などで培ってきた鋳造技術があり、金型への知見は豊富。これらにより、型交換に必要なリードタイムを約20分にまで短縮したという。これこそトヨタ創業以来の無から有を生みだすスタートアップの力とトヨタ生産方式(TPS)の融合によるカイゼンの一例と言えるだろう。
2021年に貞宝工場の一角に開設されたスタートアップスタジオ。
今回、公開された3工場を回り感じたことは、トヨタの工場は普通の自動車工場とは大きく雰囲気が異なるということだ。2021年に貞宝工場の一角に開設されたスタートアップスタジオをはじめ、一部の工場ではオフィスデスクと生産ラインが密接に並び、中にはラウンジもありメンバー同士が意見交換を行い、すぐにモノづくりにフィードバックしていく、まるでベンチャー企業のような風景が広がっていたのだ。「工場の風景を変え、クルマの未来を変えていく」。今回のワークショップのテーマを実感した瞬間だった。
挨拶の最後に新郷 和晃CPOは、CPOとしての決意を次のように宣言した。「トヨタの持つ技とデジタル・革新技術で、工程 1/2 を実現します。また開発と生産の垣根をなくし、 新しいモビリティをすばやく提供します。そして工場カーボンニュートラルや物流などモノづくりの基盤の課題解決にも取り組んでいきます」。この変革の中で、どんな新しいクルマが生まれてくるのか、その時はもうすぐそこまで来ている。
※掲載内容は公開日時点のものであり、将来にわたってその真正性を保証するものでないこと、公開後の時間経過等に伴って内容に不備が生じる可能性があることをご了承ください。※特別な表記がないかぎり、価格情報は税込です。
最新の関連記事(トヨタ)
防音断熱や車内クーラーなど車中泊仕様の基本装備が充実! RVビッグフットは埼玉県東松山市と北海道函館市に店舗を構えるキャンピングカー専門店で、自社開発のキャンピングカーのラインナップも充実。 バンコン[…]
シエンタ:モデル概要 トヨタ・シエンタは、全長4.3m弱のコンパクトな車体に3列シートを効率的に配置し、多人数乗車を可能にしたモデル。2022年にデビューした現行型は、初代モデルで高く評価されていた“[…]
もともと4WDはレース目的で造り出された駆動システムだった 4WDというとヘビーデューティなジープタイプのクルマを連想するが、ガソリンエンジン世界初の4WDはヒルクライムレースのために造り出されたもの[…]
トヨタ マークII/チェイサー/クレスタ[X70] デビュー:1984年8月 ボディカラーは”スーパーホワイト”ほぼ一択”だ。ワインレッドの内装に、柔らかなシート表皮。どこか昭和のスナックを思い起こさ[…]
コンパクトサイズが生む絶妙な取り回し タウンエースをベースにした「Plaything Ace SP」は、軽キャンピングカーより余裕があり、ハイエースよりもコンパクトという絶妙に使いやすい車両だ。全長4[…]
人気記事ランキング(全体)
専用デカールを貼ることで、仕事も遊びもこなすエブリイに変身 特別仕様車「Jリミテッド」は、「エブリイ JOIN ターボ」をベースに、専用のデカールやガンメタリック塗装のホイールキャップを追加。さらに専[…]
防音断熱や車内クーラーなど車中泊仕様の基本装備が充実! RVビッグフットは埼玉県東松山市と北海道函館市に店舗を構えるキャンピングカー専門店で、自社開発のキャンピングカーのラインナップも充実。 バンコン[…]
ミラー上部にジャストフィット! 純正パーツのようにハマる高性能デジタルランドメーター 様々なカー用品をリリースするカーメイトから、新たにリリースされた高性能ランドメーターを紹介しよう。このアイテムは、[…]
家族で楽しむ週末に寄り添うキャンピングカー LUANAが目指したのは、日常とアウトドアをシームレスにつなぐ存在。平日は街乗りに便利なバンとして使え、週末になればそのままキャンピングカーへと姿を変える。[…]
最初期のヘッドライトは、灯油を燃やすランプ式 クルマにヘッドライトが装着され出したのは1890年頃です。初期の頃は灯油を燃やして光源としていました。その後明るさを高めたアセチレンガスを燃料としたランプ[…]
最新の投稿記事(全体)
人気のAMGスタイルで、1ランク上のモデルに仕上げた特別仕様車 メルセデス・ベンツGLBは、2021年に国内導入されたモデルで、究極のオフローダーであるGクラスからインスピレーションを受けたスクエアな[…]
専用カラーの「グリ マーキュリー」「エリクサーレッド」の2色を展開 今回導入される「C4 MAX HYBRID Edition Lumière」は、「C4 MAX HYBRID」をベースモデルにサンル[…]
WLTCモードでの燃費は21.5km/Lを達成 今回導入されるプジョー2008 GT Hybridは、新開発の1.2L直列3気筒ガソリンターボエンジンに、電動モーターを内蔵した6速デュアルクラッチ式ト[…]
室内空間と視界を改善。より親しまれるスーパーハイトワゴンに進化 新型「eKスペース」は、日常を安全・安心かつ快適に過ごせる「私の日常に安らぎが寄り添うクルマ」というコンセプトを踏襲し、全方位で進化。タ[…]
唯一無二の魅力をさらに磨いて、機能も大幅アップデート! デリカミニは、2023年5月に「eKクロススペース」の実質的な後継モデルとして誕生した、SUVルックが特徴の軽スーパーハイトワゴンだ。今回のモデ[…]
- 1
- 2