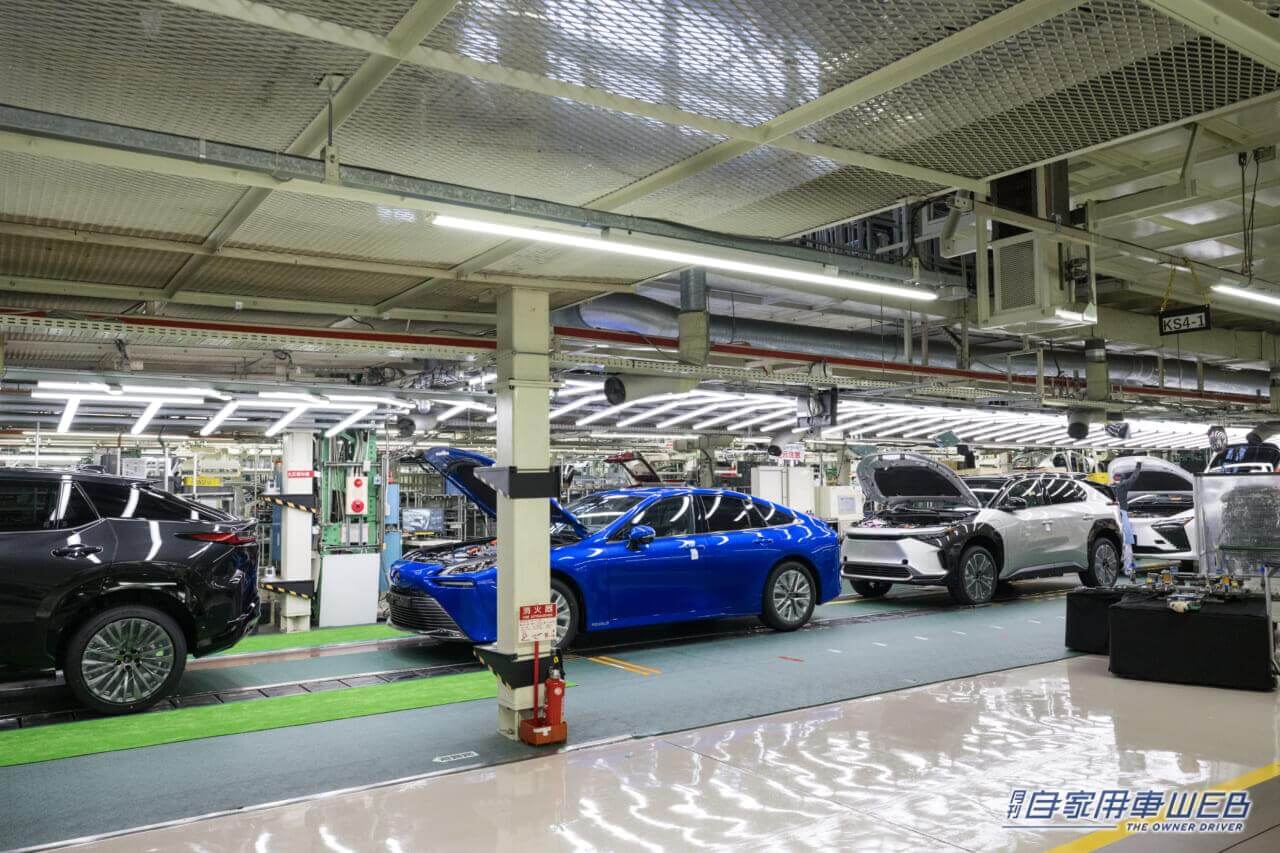
トヨタには「モノづくりは人づくり」という考え方がある。9月19日に公開された「トヨタモノづくりワークショップ」では、完成車工場である「元町工場」の混流生産ラインを支える人づくりとトヨタものづくりのスタートアップ拠点である「貞宝工場」のデジタルを活用した匠の技能の継承が紹介された。
●文:月刊自家用車編集部
どんなパワートレーンでも、どんなクルマの形でもスムーズに生産する混流生産。マルチパスウェイを支えるのは、様々な現場の知恵と工夫
トヨタ自動車が進めるマルチパスウェイは、販売地域の事情に合わせて最適なパワートレーンを販売するというもの。その種類はガソリンエンジンからHEV、FCHV、BEVと幅広い。そのマルチパスウェイ戦略を支えるのが「元町工場」の混流生産ラインだ。さらに生産されるボディタイプも様々で、セダンからミニバン、SUVとこれまた幅広い。
具体的な車名を紹介すると「元町工場」では、FCEVセダンのトヨタ「MIRAI」、ミニバンのトヨタ「ノア/ヴォクシー」のHEV、「クラウンクロスオーバー」のHEV、BEVのトヨタ「bZ4X」/スバル「ソルテラ」、レクサス「RZ」、そして旧型クラウンベースのパトカーが生産されている。さらにHEVとFCEVを搭載する新型「クラウンセダン」の生産も計画中とのこと。
「元町工場」の組立ラインは、FCEVの「MIRAI」への高圧水素タンク組み付けが専用工程になる以外、基本的にどのクルマも同じラインを流れて生産される。各種異なるパワートレーンは、積載ポイントを脱着式で入れ替えるだけで対応する汎用のトレーを採用している。
BEVのトヨタ「bZ4X」/スバル「ソルテラ」の電池パック組立工程も同一ラインにあり、BEV以外のクルマもここを一度は通過する。将来的に他車種がBEV化されても対応可能とのことで、まさに生産ラインでマルチパスウェイが成立しているのだ。
このように現状4つのパワートレーンと3つのボディタイプ、計8モデルが生産されているが、その実現のために、多彩な現場の知恵と工夫が活用されている。まず、生産にあたりクルマの構造差(組立作業時間が異なる)への対応として、作業時間の長いクルマを連続して作るのではなく、平準化をベースとした混流生産としている。
作業位置の高さを柔軟に変えられる部品や工具を載せるワゴン台車と一体化した移動式踏み台。
その平準化のための工夫の一つが「からくり」を使った様々な組立補助器具だ。サイズが異なる車種への組付け作業を行う時に、作業位置の高さを柔軟に変えられる部品や工具を載せるワゴン台車と一体化した移動式踏み台が使われている。車両後方の組み付け作業などで、車種により高さや奥行きが異なり作業がしにくくなるが、これ使うことで体への負担が減り作業が楽になっただけでなく、目視で作業ポイントが確認できるようになり作業の品質も向上したという。
ステアリングの動きを車輪に伝えるインターミディエイトシャフトの一次置き場。
もう一つ、「元町工場」組立ラインの見学で目にとまったのが、ステアリングの動きを車輪に伝えるインターミディエイトシャフトの一次置き場だ。部品を載せるとトレイが自重でスライドして作業位置まで移動し、部品回収を確認してストッパーを解除すると元の位置に戻る仕組みで動滑車の原理を使用。大きな部品を持って移動すると部品を傷つけるだけでなく、他の作業員と接触する可能性もあったという。これも「からくり」を使った工夫でカイゼンを行った一例だ。
黄色と緑色に塗り分けられている組立ラインの床面。
さらに組立ラインの床面が黄色と緑色に塗り分けられているのにも注目だ。これは車両を吊り下げるハンガーに接触し、作業員に怪我をさせないように危険が視覚的にわかる黄色に塗ったが、他の場所と比べて70ルクス明るくなるという副産物も手に入れたという。クルマの床下から作業する場合、ブラックなどダーク系のボディカラーのクルマでは細かい作業がしにくいというのがあり、過去は蛍光灯を床に付けたりヘルメットにライトを付けて作業していたが、かえって見えにくいということがあったという。しかし、黄色塗装することで安全と作業のし易さの両立ができたのだ。これもカイゼンから生まれた作業効率の進化だ。
このように車両生産のマルチパスウェイを目指し、知恵と工夫で、日々カイゼンを行い、誰かの仕事を楽に、誰かの困りごとを解決することが混流生産ラインを支えているのだ。
匠の技能をデジタルで見える化し、そのツールも自社開発。人材育成に活用し、高技能でモノづくりを進化させる
シーラー塗布工程のデモンストレーション。
”暗黙知”という言葉がある。長年の経験やノウハウなど、直感やコツ、ノウハウのことを意味する。トヨタでは、このような”暗黙知”である技能をデジタルで見える化し、継承と進化させる取り組みが行われている。
その一例が組立ラインでのシーラー塗布工程だ。防水、防錆、防音のためシーラー塗布は専用工具のシーラーガンを使って作業が行われる。例えばドアの縁に塗っていく場合、一筆書きのように均一に塗る必要がある。ムラがあってもいけなし、途切れてもいけない。
バーチャル上でシーラー塗布の訓練が行える。
この技能は多くが”暗黙知”であり、言葉だけでは伝えられず、ましてやコツをつかむことも難しい。さらに技能者の育成には時間がかかり、指導できる技能者の数も限られている。そこでトヨタはシーラーガンに多くのセンサーを取り付け、高技能者の作業をデジタルデータとして取り込み、技能を次世代に継承するツールを開発した。
具体的には、VRゴーグルを使い、センサー付きのシーラーガンとバーチャル空間を組み合わせ、匠の技能をトレースすることができるというもの。このツールを使うようになってから技能習得工数が11時間だったのが、1.9時間まで短縮され大きな効果が出ているという。なによりもバーチャル上での技能習得に対し、若い訓練者が楽しんで参加しているのも工数短縮に繋がっているという。
トヨタでは、このようなデジタルを活用した技能 ‘’継承’’を効率的に行いながらさらに人の技能を磨き、人の技能をロボットへ移植して自動化していくという。また、シーラー塗布だけでなく、鋳造、板金、溶接、塗装、組立にも展開していくことを検討している。
ここだけ切り取ると、匠の技能をデジタルで読み取って、自動化して終わりと思われるかもしれないが、そうではない。労働者不足や教えられる人の減少、習得時間の減少という厳しい状況の中、デジタルを活用して技能者も進化し自動化されたロボットも進化する。トヨタは、良い意味での人とデジタルの切磋琢磨でモノづくりを進化させ続けようとしているのだ。
※掲載内容は公開日時点のものであり、将来にわたってその真正性を保証するものでないこと、公開後の時間経過等に伴って内容に不備が生じる可能性があることをご了承ください。※特別な表記がないかぎり、価格情報は税込です。
最新の関連記事(トヨタ)
専用装備でスポーツ性能も強化 「RZ“Yellow Limited”」は、2015年に発売された86特別仕様車「GT”Yellow Limited”」と同じ「サンライズイエロー」をボディカラーに採用し[…]
子どもとのお出かけがより安心安全に! このカメラキットは、左側の死角をモニターに映し出すことで、安全運転をサポートするとても便利で有効なアイテム。車種専用の設計が施されているため目立たずスマートに装着[…]
ファミリーで過ごす時間を大切にする空間づくり 「Walk Type-A」は、家族や仲間と過ごす時間を軸に設計されたキャンピングカーで、間仕切りを極力なくした開放的な室内が特徴。広々としたダイニングスペ[…]
「水素を使う」アクションで、水素社会実現を目指す 東京都が9月3日に発足させた「TOKYO H2」は、“水素で世界をリードする東京”を目指す、官民連携で進めるプロジェクト。このプロジェクトは、タクシー[…]
軽キャンピングカー「Chippy」 キャンパー厚木といえば、人気の「Puppyシリーズ」で知られるビルダー。その経験を活かして送り出したのが軽キャンパー「Chippy」だ。従来の軽キャンピングカーが抱[…]
人気記事ランキング(全体)
ファミリーで過ごす時間を大切にする空間づくり 「Walk Type-A」は、家族や仲間と過ごす時間を軸に設計されたキャンピングカーで、間仕切りを極力なくした開放的な室内が特徴。広々としたダイニングスペ[…]
優雅な大人のクルマ旅が楽しめる軽キャンパー バンテックは埼玉県所沢市に本社を構え、キャンピングカーの製造•販売を展開。『快適で安全』を理念にオリジナルモデルを開発している。 キャブコンなど比較的大型の[…]
洗練された”ふたりのくるま旅”を演出する創業40周年記念モデル リンエイプロダクトが手掛ける最新のキャンピングカー「ファシールバカンチェス ダイネット40」は、創業40周年を記念する特別なモデルであり[…]
環境性能を重視したキャンピングカー ACSリトルノオクタービアMは、キャンピングカーの中でも特に環境性能を意識したモデルとなっている。標準で搭載される太陽光発電システムは200Wのソーラーパネルを2枚[…]
サニーに代わるエントリーカーとして開発 日本が高度経済成長期に入って庶民にも“マイカー”が浸透し始めた1960年代には、日産を代表する大衆車の「サニー」が登場します。 この「サニー」は、ほぼ同時期に発[…]
最新の投稿記事(全体)
正式発表を前に、先行情報を順次公開予定 サーキットで磨き上げたマツダの技術と情熱が注ぎ込まれるスペシャルモデル「マツダスピリットレーシング」は、S耐で得た知見が注がれた特別なモデルとして注目を集めてい[…]
専用装備でスポーツ性能も強化 「RZ“Yellow Limited”」は、2015年に発売された86特別仕様車「GT”Yellow Limited”」と同じ「サンライズイエロー」をボディカラーに採用し[…]
9月13日に富士スピードウェイで実車もお披露目 スバルBRZ「STI Sport YELLOW EDITION」は、「STI Sport」をベースにした特別仕様車。 ボディカラーには「サンライズイエロ[…]
艶やかなグロッシーブラックのエクステリアパーツを採用 特別仕様車「XC40 Dark Edition」は、フロントグリルをはじめとする各所にグロッシーブラックのエクステリアパーツを採用し、スポーティな[…]
ホンダの車内快適化計画、中古車向け「フロアカーペットマット」の価格を改定 ホンダアクセスが、中古車向け純正「フロアカーペットマット」の価格を改定した。2011年以降に販売されたN-BOX、フィット、ス[…]
- 1
- 2