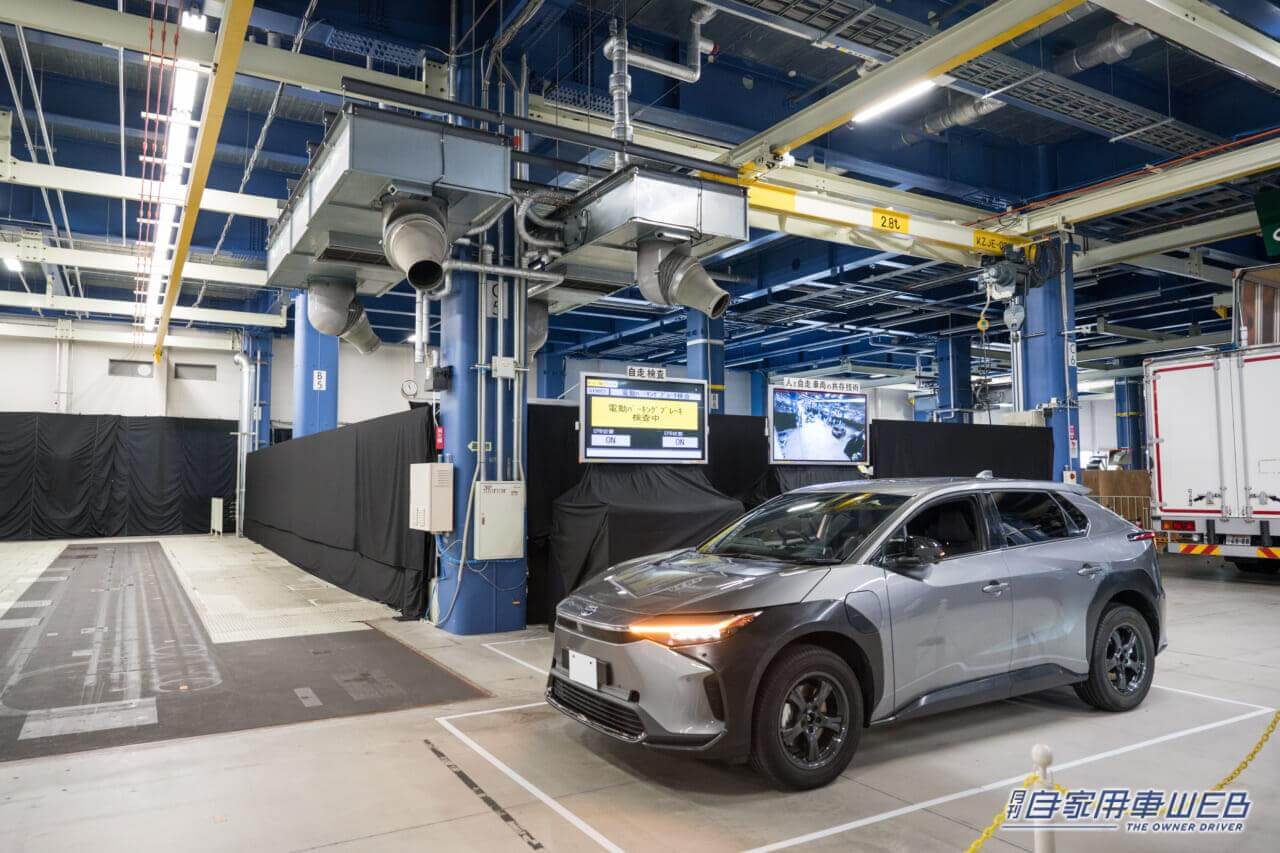
9月19日に公開された「トヨタモノづくりワークショップ」では、次世代BEVの開発へ向けた取り組みが数多く公開された。トヨタでは2026年に航続距離1000㎞を目指した次世代BEVの市場投入を目指している。今回は、それを裏付ける、リードタイムを短縮し、進化する生産現場の現状を見ることができた。
●文:月刊自家用車編集部
BEVの適時投入を目指して、デジタルツインの導入や作業の効率化、生産性の向上で新しいモノづくりにチャレンジ
2023年6月に公開された「トヨタテクニカルワークショップ」で、2026年からの次世代BEVの市場投入を明言したトヨタ。2027年までに航続距離1000㎞を実現するパフォーマンス版次世代電池や良品廉価な普及版次世代電池、そしてBEV用全固体電池についても2027〜2028年実用化へのチャレンジや車体をシンプルスリムな構造にするギガキャストについても導入が公表された。
今回の「トヨタのモノづくりワークショップ」では、これら次世代技術の量産へ向けた取り組みが公開された。「貞宝工場」、「明知工場」、「元町工場」で進む次世代モノづくりの状況を見ていこう。
現場の知恵が設計段階で3Dモデルに落とし込まれ、完成度の高い設備をやり直しをしなくても現場に導入できるようになった。
現在、トヨタでは次世代BEVの投入に向けて、開発から生産までの時間短縮、つまりリードタイムの短縮に向けて総力で取り組んでいる。その代表格が、生産設備づくりのデジタルツイン活用だ。デジタルツインとは現実の空間をデジタル上にコピーしたもので、トヨタは生産設備の3Dモデルを製作。1/1の縮尺で画面やVRを使った検討により、設備の設計担当、製造担当、実際に設備を使う作業者が、事前に不具合を洗い出せるようになったという。
これらの取り組みで、現場の知恵が設計段階で3Dモデルに落とし込まれ、完成度の高い設備をやり直しをしなくても現場に導入できるようになり、設計から生産開始までのリードタイムは半分になったという。さらに海外工場ともオンラインで検討を行うことで、リアルシミュレーションが可能になり効率が上がっているとのこと。
トヨタ「貞宝工場」の金型・設備部品加工設備では、これまで人に頼っていた材料投入などの作業を、3Dモデル上で改善し自動化。それを実際の設備に反映させることで、生産性が3倍、従来比での改善リードタイム3分の1を実現したという。
「貞宝工場」では、次世代電池普及版バイポーラ型リチウムイオン電池と全固体電池の開発ラインも稼働している。
6月のテクニカルワークショップで公開された次世代電池群。
「貞宝工場」の全固体電池の開発ライン。
次世代電池普及版バイポーラ型リチウムイオン電池は、2026〜27 年の実用化に向けて、製品開発や量産工法の確立が進んでいる。今回、工法の一部として塗工行程が公開された。塗工行程では、安価なリン酸鉄リチウム(LFP)の性能を最大限に引き出すために、そのペーストをムラなく大量に金属箔に塗る必要がある。均一にかつ高速に厚く綺麗に塗る必要があるが、HEVなどで培った長年の電池生産の経験と、FC(燃料電池)で開発した高速の間欠塗工を応用した設備が導入され、試験生産がスタートしていた。
BEV用全固体電池についても、2027〜28 年の実用化に向けた製品開発や量産工法の開発に取り組んでいる。今回、量産を見据えた高速かつ高精度スピードで、 電池素材へのダメージなく積み重ねるという難しい工法の現状が公開された。全固体電池は液系電池とは異なり、負極、正極、固体電解層がそれ ぞれ隙間なく密着している状態が理想だ。これをメカニカルな”からくり”の応用と同期制御で実現した工法を見ることができた。
右が6月のテクニカルワークショップで公開されたギガキャストで作られたリヤモジュール。左は従来の板金部品で構成。
「明知工場」のギガキャストの試作用設備。
さらに「明知工場」では、ギガキャストの試作用設備が公開された。ギガキャストとは、従来数十点の板金部品で作っていたものを、アルミダイキャストで一体成形する技術。今回、実際の製造工程を見ることができたほか、ギガキャストで必要な定期的な鋳造の型の交換についても通常24時間程度必要なところ、素早い金型交換が可能な金型を開発し、型交換に必要なリードタイムを約20分にまで短縮。これはトヨタの今まで培ってきた鍛造技術や低圧成形やダイキャストに用いる金型への知見が活かされたという。ギガキャストについては、BEVのbZ4Xに搭載して走行テストを開始していることも公表された。
「元町工場」の次世代BEV実証ライン。
そして次世代BEVの生産ラインの準備状況についても一部が公開された。「元町工場」では、すでに自動運転開発で培ってきた制御技術と工場に設置されたセンサーによる人、車と環境の認識技術を組み合わせて完成車の自動搬送を実現している。これを応用し、次世代BEV実証ラインを設置。0.36㎞/hというコンベアに近い、極低速での安定した走行を可能とし、製品自らが移動する自走組立ラインの開発が進んでいる。
次世代BEVのフロント、センター、リアの3分割モジュール構造。
次世代BEVは、ギガキャストを用いた新しいモジュール構造を採用。フロント、センター、リアの3分割で、従来作業員が乗り込んで作業していた状況に比べて、最短アクセスかつオープンな環境での作業が可能となり、作業性の効率化、生産性が向上。ここでもリードタイムを短縮することができるという。
さらに次世代BEV実証ラインでは、部品を運ぶ自動フォークリフトや自動物流ロボット、重いシートなどを組み立て中の車両に載せるロボットのデモも公開された。これら工場内の自動物流を実用化することで、人材不足の解消やつらい作業をなくす取り組みも開発が進んでいる。
※掲載内容は公開日時点のものであり、将来にわたってその真正性を保証するものでないこと、公開後の時間経過等に伴って内容に不備が生じる可能性があることをご了承ください。※特別な表記がないかぎり、価格情報は税込です。
最新の関連記事(トヨタ)
専用装備でスポーツ性能も強化 「RZ“Yellow Limited”」は、2015年に発売された86特別仕様車「GT”Yellow Limited”」と同じ「サンライズイエロー」をボディカラーに採用し[…]
子どもとのお出かけがより安心安全に! このカメラキットは、左側の死角をモニターに映し出すことで、安全運転をサポートするとても便利で有効なアイテム。車種専用の設計が施されているため目立たずスマートに装着[…]
ファミリーで過ごす時間を大切にする空間づくり 「Walk Type-A」は、家族や仲間と過ごす時間を軸に設計されたキャンピングカーで、間仕切りを極力なくした開放的な室内が特徴。広々としたダイニングスペ[…]
「水素を使う」アクションで、水素社会実現を目指す 東京都が9月3日に発足させた「TOKYO H2」は、“水素で世界をリードする東京”を目指す、官民連携で進めるプロジェクト。このプロジェクトは、タクシー[…]
軽キャンピングカー「Chippy」 キャンパー厚木といえば、人気の「Puppyシリーズ」で知られるビルダー。その経験を活かして送り出したのが軽キャンパー「Chippy」だ。従来の軽キャンピングカーが抱[…]
人気記事ランキング(全体)
ファミリーで過ごす時間を大切にする空間づくり 「Walk Type-A」は、家族や仲間と過ごす時間を軸に設計されたキャンピングカーで、間仕切りを極力なくした開放的な室内が特徴。広々としたダイニングスペ[…]
優雅な大人のクルマ旅が楽しめる軽キャンパー バンテックは埼玉県所沢市に本社を構え、キャンピングカーの製造•販売を展開。『快適で安全』を理念にオリジナルモデルを開発している。 キャブコンなど比較的大型の[…]
洗練された”ふたりのくるま旅”を演出する創業40周年記念モデル リンエイプロダクトが手掛ける最新のキャンピングカー「ファシールバカンチェス ダイネット40」は、創業40周年を記念する特別なモデルであり[…]
環境性能を重視したキャンピングカー ACSリトルノオクタービアMは、キャンピングカーの中でも特に環境性能を意識したモデルとなっている。標準で搭載される太陽光発電システムは200Wのソーラーパネルを2枚[…]
サニーに代わるエントリーカーとして開発 日本が高度経済成長期に入って庶民にも“マイカー”が浸透し始めた1960年代には、日産を代表する大衆車の「サニー」が登場します。 この「サニー」は、ほぼ同時期に発[…]
最新の投稿記事(全体)
正式発表を前に、先行情報を順次公開予定 サーキットで磨き上げたマツダの技術と情熱が注ぎ込まれるスペシャルモデル「マツダスピリットレーシング」は、S耐で得た知見が注がれた特別なモデルとして注目を集めてい[…]
専用装備でスポーツ性能も強化 「RZ“Yellow Limited”」は、2015年に発売された86特別仕様車「GT”Yellow Limited”」と同じ「サンライズイエロー」をボディカラーに採用し[…]
9月13日に富士スピードウェイで実車もお披露目 スバルBRZ「STI Sport YELLOW EDITION」は、「STI Sport」をベースにした特別仕様車。 ボディカラーには「サンライズイエロ[…]
艶やかなグロッシーブラックのエクステリアパーツを採用 特別仕様車「XC40 Dark Edition」は、フロントグリルをはじめとする各所にグロッシーブラックのエクステリアパーツを採用し、スポーティな[…]
ホンダの車内快適化計画、中古車向け「フロアカーペットマット」の価格を改定 ホンダアクセスが、中古車向け純正「フロアカーペットマット」の価格を改定した。2011年以降に販売されたN-BOX、フィット、ス[…]
- 1
- 2