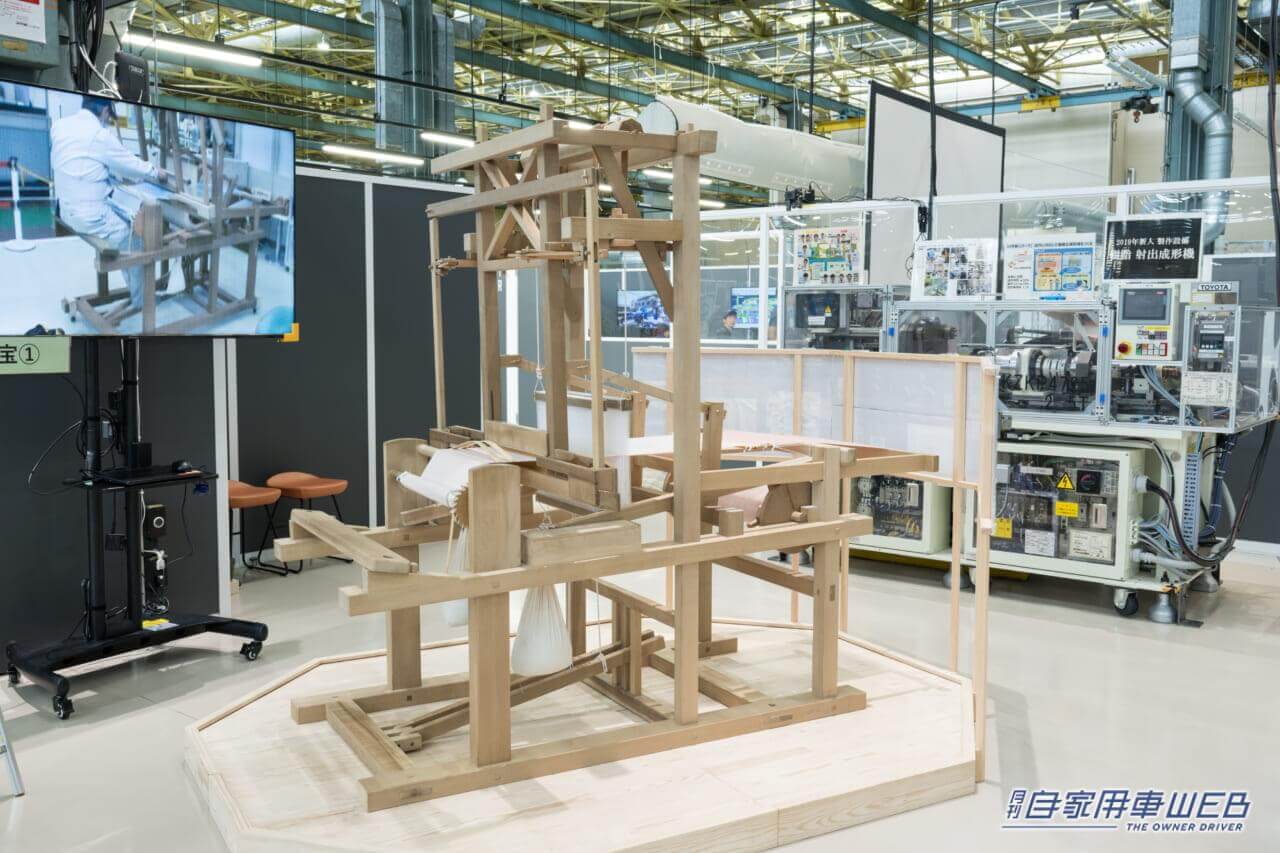
「クルマづくりの未来を変えていこう」をテーマにモノ作りの現場を公開したトヨタ自動車。この「トヨタのモノづくりワークショップ」では、トヨタそのものの原点である、「自分以外の誰かのために」がどうやって具現化されているのか?をつぶさに見ることができた。「貞宝工場」、「明知工場」、「元町工場」で行われている取り組みをリポートする。
●文:月刊自家用車編集部
無から有を生み出すために、「知恵と工夫」「匠の技」と「革新技術」「デジタル」を融合
トヨタは、創業以来から同じ想いを共有した仲間が現場に集まり、知恵を出し合って創意工夫を行い、高い技能を通じて新しいモノを生み出し、量産化してきた。その原点は、トヨタグループ創始者である豊田佐吉氏までさかのぼる。佐吉氏は「毎晩、夜なべをして機織り仕事をする母を助けたい、少しでもその仕事を楽にできないか」との想いから人力織機を開発した。その想いはまさに「自分以外の誰かのために」である。
その後、佐吉氏の息子である喜一郎氏が設立した豊田自動織機 自動車部(現 トヨタ自動車)は、当時、材料も資金も十分でなかった状況で創意工夫を凝らし、自働化とジャストインタイムという二つの考え方を導入して、後のトヨタ生産方式(TPS)と呼ばれる「人中心のモノづくり」の基盤をつくりあげた。
「貞宝工場」のスタートアップスタジオ。
今回の取材で一番最初に訪れた「貞宝工場」は、トヨタものづくりのスタートアップ拠点だ。無から有を生み出す開発の現場であり、「知恵と工夫」/「匠の技」と「革新技術」/「デジタル」でアイデアを素早くカタチにするプロセスを担っている。
今回のワークショップで初公開となった「貞宝工場」のスタートアップスタジオは、「モビリティカンパニーへのフルモデルチェンジ=クルマづくりの未来を変える」ために2021年に開設。メンバー同士が意見交換を行えるラウンジと、すぐ横にモノづくり工房を置くことで、アイデアをスピーディに具現化して、試作開発から量産技術開発まで取り組める環境が整備されている。その様はスタートアップ企業、いやベンチャー企業か? というほどアクティブな環境だった。
HEVモーターの手作り試作品。
このスタートアップスタジオでの取り組みの一例としてHEVモーターの手作り試作品を展示。さらにこれらの製品を製造するための設備開発まで行っていることも公開された。その内容はHEVのバッテリーやFCEVの水素タンクまでに及び、最初はポンチ絵と呼ばれる構想図からスタートし、手治具を製作。形にしたものを量産へつなげるというものだ。
板金の匠が製作したスチール製のグローブやボール、洋兜。
さらには、「匠工房」と呼ばれる、匠の板金技能を進化させて魅力的な商品を生み出す活動も行っている。匠とその後輩が設計図のないところから材料の限界までチャレンジしながら、創作物を制作することでその技術を継承。スチール製のグローブやボール、洋兜などが展示されており、その精巧さは舌を巻くどころのレベルではない。これらの技術は、新たな商品づくり、人づくりに活かされているという。
これら匠の技術は、ロボットではできない繊細な作業や高品質な製品仕上げでその真価を発揮する。その一例が、「明知工場」で公開されたレースで勝つために求められる厳しい性能要求に応える匠の技だ。
モータースポーツ用超高性能エンジン。
トヨタではモータースポーツにおいて、スーパーフォーミュラ、SUPER GTのGT500クラス、WRC FIA世界ラリー選手権、WEC FIA世界耐久選手権、北米のNASCAR参戦車両のエンジンを供給している。これら超高性能エンジンの主要な鍛造部品はすべてトヨタ内製で提供しているが、その非常に複雑な内部構造は、鋳物の中空部を作るための中子(なかご)を用いて成形されている。
量産エンジン用の中子(なかご)。最終調整は匠の手作業となる。
モータースポーツ用超高性能エンジンでは、高強度/高精度/複雑形状対応が要求され、そのパーツ点数も量産エンジンの2倍から3倍となり、それによって中子(なかご)も複雑になるという。そこで匠と呼ばれる高い技能を持つモノづくりのプロフェッショナルの出番となる。匠による中子(なかご)の造形技術により 1g 単位で調整されているのだ。
この中子(なかご)を製作する際の木型製作のプロセスにおいても、匠の知識と経験が生かされている。工程設計や部品構成の検討や設計において3Dモデルを使ったデジタルが導入されているが、形状と機能の高度な読解力と高度な技能を継承させるため、人材育成が行われている。それはデジタル化の時代でも、匠の技能がそれを上回ることがあるからだという。匠の手加工とデジタル技術を組み合わせることで、設計変更のリードタイムも大幅に短くなった。
匠のアルミ鋳造技術により実現した超高性能エンジンは、レースの現場で鍛え上げられる。壊しては、直すの繰り返しで人とクルマを鍛え、ル・マン24時間レース5連覇という偉業を成し遂げた礎ともなっているのだ。この知見は、量産車にも反映されており、モータースポーツを起点とした”もっといいクルマづくり”の裏には、匠の技能があるのだ。
さらに新車組み立て工場である「元町工場」における匠の加工技術を見ていこう。現在、匠の技・加工技術の進化により、これまで困難とされてきた高い意匠性と機能性を実現できるようになってきており、今後は量産車でありながら、顧客一人一人の好みに合わせ、個性のあるクルマを提供していきたい、としている。
今回その取り組みの事例として「ピアノブラック調バンパーの塗装レス化技術」、「樹脂バンパーのインクリメンタル成形技術」、「シャープなキャラクターラインを成形するレーザー加工技術」、「精巧な槌目(つちめ)模様を入れる匠の板金性能」の4つが紹介された。
「ピアノブラック調バンパーの塗装レス化技術」は、近日登場予定の「トヨタ・クラウンスポーツ」から導入される技術。金型側を匠の技で鏡のように傷一つなく均一に磨き上げることで、塗装なしの素材本来の色で艶のあるピアノブラックカラーのバンパーが量産できるようになったという。多少のキズは拭き取りで落ちるので、補修性が向上したほか、塗装が不要になることで、塗装作業で発生するCO2排出が削減され、工場のカーボンニュートラルにも貢献する。
次に6月に発売された「レクサスLC」の限定・特別仕様車“EDGE”に採用された空力性能を向上させる一体成型バンパーカナードだ。「樹脂バンパーのインクリメンタル成形技術」が採用されており、棒状の工具を連続的に材料に押し付けて成形する工法で、従来は金属のみに適用されていた技術だが、新たに樹脂への工法を開発した。通常カナードは別部品として取り付けられるが、バンパーに追加の加工を施すことでシームレスなデザインを実現している。
そして、9月に発表されたばかりの新しい「センチュリー」に採用されている「シャープなキャラクターラインを成形するレーザー加工技術」、「精巧な槌目(つちめ)模様を入れる匠の板金性能」だ。
「シャープなキャラクターラインを成形するレーザー加工技術」は、プレス成形後に追加でレーザー加工をすることで、 シャープなキャラクターラインを成形する技術だ。従来車にも採用されているが、新しい「センチュリー」では、ルーフラインに採用されている。これは、従来プレス成形で造られるキャラクターラインが、形状と部位によってはシャープな線が造れない部分を、プレス成型後に追加でレーザー加工するというもの。もともとはレザー溶接時の失敗から生まれたというが、そういったことも取り込んでしまうのがトヨタの匠。新しい「センチュリー」の場合、ルーフの前方がレーザー加工で、後半がプレス成型。その境目は、レーザーの出力を微調整しながら馴染ませているというのだから驚きだ。実車に触れたが、当然まったくその境目は分からなかった。
さらに匠の技を惜しみなく投入したのが、新しいセンチュリー向けの用品として提供される手作りの「スカッフプレート」だ。「精巧な槌目(つちめ)模様を入れる匠の板金性能」が採用され、試作車作りを通じて継承されてきたハンマーによる板金技能が活かされている。薄いステンレ ス板を歪ませる事なく、材料の伸びを意識しながら数千点打刻していく技能により、「柾目(まさめ)」と呼ばれる木の模様を表現する。匠が手加工で一つずつ打痕していくという工芸品である。
このように匠の技は、エンジンなどのクルマの心臓部などの製造、そして造形技術、素材の加工技術まで多岐に及ぶ。まさにトヨタモノづくりの原点であり、要。そして今あるトヨタ/レクサスのクルマにはもちろん、今後発売される新型車にも採用される、現在進行形で常に進化していく「技」、なのである。この「技」をデジタルで進化させ、またその「技」を匠が進化させる。トヨタの生産現場は、急速にリードタイムを短縮しながら、クルマづくりの「技」を磨き上げていることが実感できた工場取材だった。
※掲載内容は公開日時点のものであり、将来にわたってその真正性を保証するものでないこと、公開後の時間経過等に伴って内容に不備が生じる可能性があることをご了承ください。※特別な表記がないかぎり、価格情報は税込です。
最新の関連記事(トヨタ)
専用装備でスポーツ性能も強化 「RZ“Yellow Limited”」は、2015年に発売された86特別仕様車「GT”Yellow Limited”」と同じ「サンライズイエロー」をボディカラーに採用し[…]
子どもとのお出かけがより安心安全に! このカメラキットは、左側の死角をモニターに映し出すことで、安全運転をサポートするとても便利で有効なアイテム。車種専用の設計が施されているため目立たずスマートに装着[…]
ファミリーで過ごす時間を大切にする空間づくり 「Walk Type-A」は、家族や仲間と過ごす時間を軸に設計されたキャンピングカーで、間仕切りを極力なくした開放的な室内が特徴。広々としたダイニングスペ[…]
「水素を使う」アクションで、水素社会実現を目指す 東京都が9月3日に発足させた「TOKYO H2」は、“水素で世界をリードする東京”を目指す、官民連携で進めるプロジェクト。このプロジェクトは、タクシー[…]
軽キャンピングカー「Chippy」 キャンパー厚木といえば、人気の「Puppyシリーズ」で知られるビルダー。その経験を活かして送り出したのが軽キャンパー「Chippy」だ。従来の軽キャンピングカーが抱[…]
人気記事ランキング(全体)
ファミリーで過ごす時間を大切にする空間づくり 「Walk Type-A」は、家族や仲間と過ごす時間を軸に設計されたキャンピングカーで、間仕切りを極力なくした開放的な室内が特徴。広々としたダイニングスペ[…]
優雅な大人のクルマ旅が楽しめる軽キャンパー バンテックは埼玉県所沢市に本社を構え、キャンピングカーの製造•販売を展開。『快適で安全』を理念にオリジナルモデルを開発している。 キャブコンなど比較的大型の[…]
洗練された”ふたりのくるま旅”を演出する創業40周年記念モデル リンエイプロダクトが手掛ける最新のキャンピングカー「ファシールバカンチェス ダイネット40」は、創業40周年を記念する特別なモデルであり[…]
環境性能を重視したキャンピングカー ACSリトルノオクタービアMは、キャンピングカーの中でも特に環境性能を意識したモデルとなっている。標準で搭載される太陽光発電システムは200Wのソーラーパネルを2枚[…]
サニーに代わるエントリーカーとして開発 日本が高度経済成長期に入って庶民にも“マイカー”が浸透し始めた1960年代には、日産を代表する大衆車の「サニー」が登場します。 この「サニー」は、ほぼ同時期に発[…]
最新の投稿記事(全体)
正式発表を前に、先行情報を順次公開予定 サーキットで磨き上げたマツダの技術と情熱が注ぎ込まれるスペシャルモデル「マツダスピリットレーシング」は、S耐で得た知見が注がれた特別なモデルとして注目を集めてい[…]
専用装備でスポーツ性能も強化 「RZ“Yellow Limited”」は、2015年に発売された86特別仕様車「GT”Yellow Limited”」と同じ「サンライズイエロー」をボディカラーに採用し[…]
9月13日に富士スピードウェイで実車もお披露目 スバルBRZ「STI Sport YELLOW EDITION」は、「STI Sport」をベースにした特別仕様車。 ボディカラーには「サンライズイエロ[…]
艶やかなグロッシーブラックのエクステリアパーツを採用 特別仕様車「XC40 Dark Edition」は、フロントグリルをはじめとする各所にグロッシーブラックのエクステリアパーツを採用し、スポーティな[…]
ホンダの車内快適化計画、中古車向け「フロアカーペットマット」の価格を改定 ホンダアクセスが、中古車向け純正「フロアカーペットマット」の価格を改定した。2011年以降に販売されたN-BOX、フィット、ス[…]
- 1
- 2