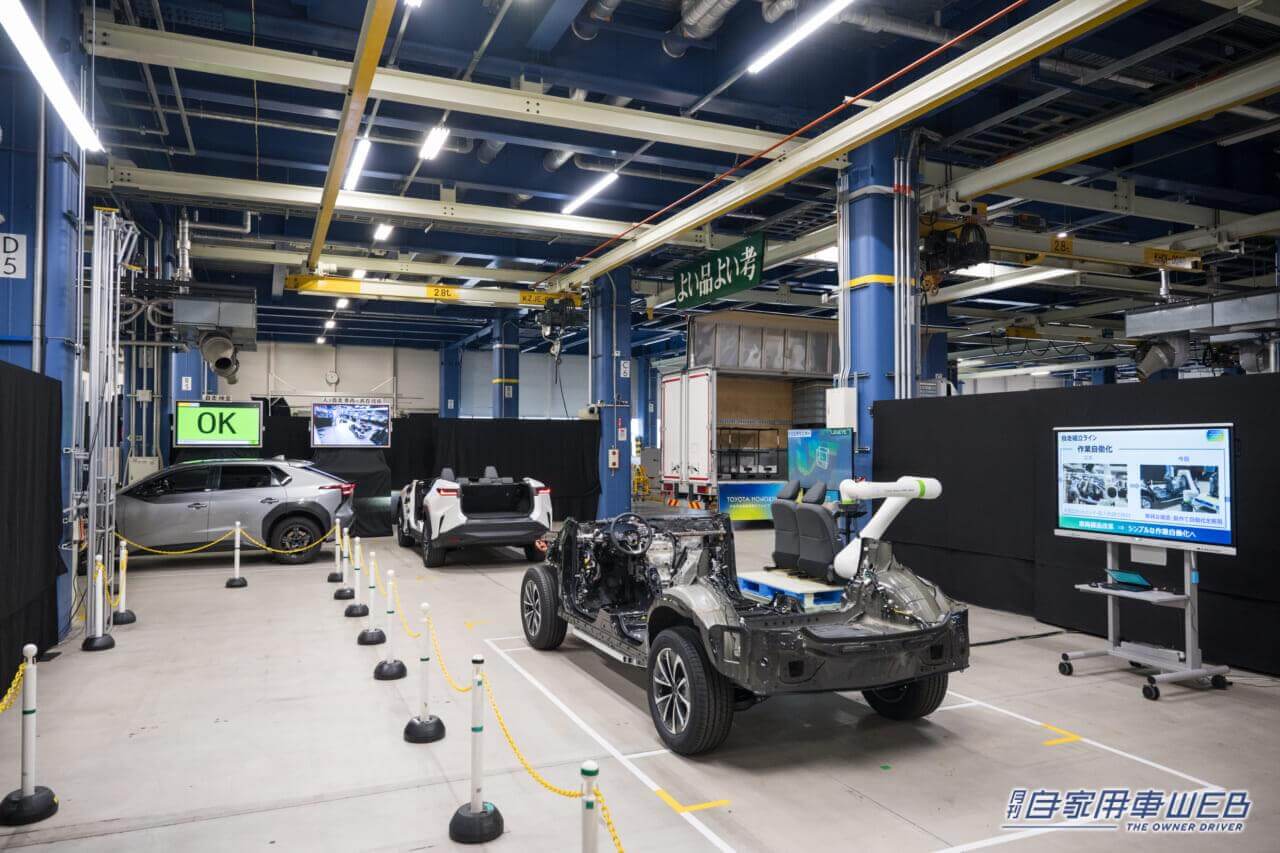
トヨタ自動車株式会社は、愛知県にある同社の貞宝工場、明知工場、元町工場で取り組まれている様々なモノづくり技術を「トヨタモノづくりワークショップ」としてメディアに公開。初公開となる、デジタルと革新技術でTPS(トヨタ生産方式)と現場力を進化させ、“もっといいクルマ”を生み出す原動力を見ることができた。
●文:山本シンヤ ●写真:トヨタ自動車株式会社
理念は「幸せの量産」。「未来を形にする」ための取り組みを大公開
ワークショップ冒頭で挨拶に立った執行役員Chief Production Officer(CPO)の新郷 和晃氏。クルマ製造の大変革のために「トヨタの技で、モノづくりの未来を変えたい」と語る。
トヨタはこれまで開発中の情報をあまり、いやほとんどオープンにしてこなかった。それは機密の問題だけでなく「完璧な物にしないと見せられない」と言う考え方の問題だったと思う。ただ、それでは目指すべき道が不明確なのはもちろん、実現のレベルも解らなかった。つまり“アピール下手”である。それが故に、新聞や経済誌の中には「トヨタは遅れている」、「トヨタは解っていない」などの的外れな記事が世に出ている。
2021年に貞宝工場の一角に開設されたスタートアップスタジオ。ラウンジもありメンバー同士が意見交換を行い、すぐにモノづくりにフィードバックしていく。
最近で言えば「電動化」だろう。古くから開発・研究を進めているが、それは単にハード側の技術はもちろんだが、コスト低減や生産技術、更には材料の供給体制など、ビジネスを行なう上での体制づくりを着実に行なってきたが、正しい評価はされなかった。その理由は「トヨタはウンチクだけで、肝心なクルマが出てこない」だった。
「だったら全部見せるよ!!」
それが2021年の「バッテリーEVに関する説明会」だった。ここでは開発中の数多くのBEVモデルのお披露目と驚きの販売計画が発表されたが、筆者はここがトヨタの情報開示に関するターニングポイントだったと思う。「包み隠さず全てを見せる、つまり豊田章男氏が言う「トヨタは逃げない、隠さない、嘘をつかない」をリアルに実践したわけだ。その後も、「ここまで言うの!?」と逆に我々がビビるくらい、様々な情報を開示。
「貞宝工場」の全固体電池の開発ライン。全固体電池は液系電池とは異なり、負極、正極、固体電解層がそれぞれ隙間なく密着している状態が理想。メカニカルな”からくり”の応用と同期制御で実現した工法を公開。
その一つが、今年6月に開催された「トヨタ・テクニカルワークショップ」だ。佐藤恒治社長率いる新執行体制が掲げた「クルマの未来を変えていく」上での3つの重要なカギ「電動化/知能化/多様化」を実現させるための最新技術を公開。技術トップである中嶋裕樹副社長は「各領域、90%まで見せています」と語った。
ただ、トヨタの理念は「幸せの量産」だ。つまり、いくら優れた技術でも“量産”できなければ意味がない。そこに関しても抜かりなしで、9月に「トヨタ・モノづくりワークショップ」を開催。要するに「未来を形にする」ための取り組みの公開だ。
初公開された明知工場のギガキャスト試作用設備。定期的な鋳造の型の交換が必要だが、必要なリードタイムを約20分にまで短縮したという。
多くのメディアの注目は全個体電池/ギガキャスティングの試作ラインだった。確かに全個体電池は高速・高精度スピードで素材へのダメージなく生産するために「からくり」の応用と「同期制御」を用いての実現、ギガキャストは長年培ってきた鋳造技術の秘伝のレシピを活かした金型・生産に関する知見、解析技術による品質アップ、金型交換の工夫による稼働停止時間のムダ削減など、どちらも試作と言いながらも 量産を見据えたモノである。
トヨタが自ら開発して生産して生み出してきたハイブリッド用のモーター。これらの製品を製造するための設備開発まで行っていることも公開された。
ただ、筆者がより興味深く感じたのは、実は他の部分だった。それは各工場での「現地現物」と「デジタル・革新技術」の融合だ。
開発から生産までの時間短縮のため、現実の空間をデジタル上にコピーしたデジタルツインを活用。実際に設備を使う作業者が、事前に不具合を洗い出す。
貞宝工場では生産設備をデジタル上で再現しそこで検証を事前に済ませて設備をつくる……と言う取り組みを見学。生産領域トップの新郷和晃氏は「素早くやって何度もチャレンジ」と語るように、素早いビジネスだけではなくコスト削減まで可能にしているのだ。
熟練工が持つ技能をデジタルで見える化し、継承と進化させる取り組みが行われている。写真はバーチャル上で行われるシーラー塗布の訓練。
また、多くの企業が抱える後継者問題に関しても、これまで暗黙知だった匠の技術デジタル解析することで、「解りやすく」、「簡単に」、「広く」習得できるようなツールを開発。これは人材育成にも非常に役立っているそうだ。
「明知工場」ではスーパーフォーミュラ、SUPER GTのGT500クラス、WRC FIA世界ラリー選手権など参戦車両のエンジンを組み立てる。モータースポーツエンジンでは、高強度/高精度/複雑形状対応が要求され、匠による中子(なかご)の造形技術により 1g 単位で調整。
明知工場ではモノづくりの原点を見学。レース用エンジンの複雑な内部構造は匠の造形による1g単位の調整により具体化されるが、ロボットではできない繊細な作業や高品質な製品仕上げに驚いた。実はこれも未来に繋がっている。
以前、エグゼクティブフェローの河合満氏が「ある実験でロボットに美しい字を書かせるように教える際、書道未経験者が教えた場合と書道経験者が教えた場合とでは結果は歴然。つまり、トヨタ生産方式は熟練を重ねた『匠の技』をロボットに織り込むことが重要」と語ったが、そのためにも良いお手本……つまり人の技術は育て続ける必要があるのだ。
次世代BEVは、ギガキャストを用いた新しいモジュール構造を採用。フロント、センター、リヤの3分割で、作業性の効率化、生産性を向上させる。
元町工場では次世代BEVラインを見学。クルマをフロント/センター/リヤの3分割構造で考える「モジュール構造」に加えて、コンベアで搬送せず自ら走って部品が組付けられる「自走ライン」による作業の効率化・生産性向上は、今後の自動車生産工場の景色を大きく変えるかもしれない。
「元町工場」の完成車組立ライン。生産される車種やパワートレーンはガソリンエンジンからHEV、FCEV、BEVと幅広く、完全な混流生産を実現。
もちろん、大きな変化だけでなく、からくりを使った「無動力装置の活用」、「エアレス塗装」による塗装工程のコンパクト化や省資源化、水素をはじめとする再生エネルギー活用など、規模や領域を問わずカイゼン活動は行なわれている。また、大きな課題の一つである物流問題への対応として、車両搬送ロボットの実証実験なども進められていた。
新しいセンチュリー向けの用品として提供される手作りの「スカッフプレート」。匠の手作業で「柾目(まさめ)」と呼ばれる木の模様を表現。
このようにトヨタの未来は着実に実現に向けて動き始めている。その戦略は単なる付け焼刃でなく、実に計画的に行なわれているのだ。これらを見て、まだ「トヨタは遅れている」と言うメディアの人は、真実を知って、考えを改めた方がいい。そんな印象を受けた取材だった。
※掲載内容は公開日時点のものであり、将来にわたってその真正性を保証するものでないこと、公開後の時間経過等に伴って内容に不備が生じる可能性があることをご了承ください。※特別な表記がないかぎり、価格情報は税込です。
最新の関連記事(トヨタ)
タウンエースベースが生む、扱いやすさと拡張性 「Plaything Ace SP」のベース車両は、トヨタ・タウンエース。取り回しの良さと荷室の広さを両立したミドルサイズバンで、日常使いでも不便を感じに[…]
メモリアルモデルにふさわしい、特別な内外装加飾を装着 特別仕様車「“THE 70th”」は、日本の風景との調和を意識した特別なバイトーンのボディカラー(プレシャスメタル×プレシャスホワイトパールとプレ[…]
ハイエースの常識を変える。“大人2段ベッド”の実力 ハイエースのスーパーロング・ワイド・ハイルーフは確かに広い。しかし全長が5mを超えるため、都市部では駐車場に収まらないことも多い。スーパーロングでな[…]
電子制御サスペンションは、3つの制御方式に大きく分類される サスペンションに電子制御を持ち込み、走行状態、路面の状況に合わせた最適な乗り心地やアジリティ、スタビリティが得られるものも一部のクルマに採用[…]
フェイスリフトでイメージ一新。都会に映えるスタイリングへ 今回のマイナーチェンジで、フェイスリフトが実施されたカローラクロス。ボディ同色かつバンパー一体成形のハニカム状グリルが与えられたフロントマスク[…]
最新の関連記事(レクサス)
大容量ブレーキシステム&鍛造アルミで、強力なストッピングパワーを獲得 レクサスISは1999年の初代モデル誕生以来、「クルマを操る楽しさ」を追求してきたコンパクトFRスポーツセダン。これまでに世界約4[…]
1989年「レクサス」誕生。最初は「LS」と「ES」の2本立て レクサスの最初の商品は、日本では初代セルシオとして販売されたLSと、カムリのV6エンジン車、プロミネントがベースのES。LSの完成度と比[…]
過酷な道路環境を模したテストコースで得た、走りの質を高める改良を実施 レクサスLBXは、2023年12月の導入以降、60以上の国と地域で、約6.5万台(2025年3月末時点)の販売実績をもつクロスオー[…]
スピンドルグリルから「スピンドルボディ」へ。次世代デザインの到達点 ボディサイズは全長4,890mm、全幅1,920mm、ホイールベースは2,850mm。最低地上高は190~195mmに設定されており[…]
電動化を積極的に進めるレクサス。その次世代グローバルモデルのトップバッターとして登場。国内には2026年春に導入予定 初代ESは1989年の販売を開始以来、静粛性や乗り心地、広い室内空間で高い評価を得[…]
人気記事ランキング(全体)
奥まで届く薄型設計で内窓掃除が快適に 近年の車はフロントガラスの傾斜が鋭角になり、従来の内窓ワイパーでは掃除しづらいケースが増えている。特にプリウスなど一部車種ではダッシュボード付近に大きなモニターや[…]
ポップアップルーフがもたらす圧倒的な開放感 まず注目したいのは、ポップアップルーフによって実現した最大2000mmという室内高。この高さがあることで、室内で立ったまま着替えたり、作業したりすることがで[…]
引っ張るだけでOK、瞬時にセット完了 ロール式サンシェードの最大の魅力は、その操作の簡単さにある。取り付けは非常にシンプルで、工具も必要なくサンバイザーに専用パーツを固定するだけ。その状態でロール部分[…]
夏の猛暑も怖くない、ロール式サンシェードが作る快適空間 夏のドライブで誰もが感じる悩みは、車内の暑さだ。炎天下に駐車すれば、シートやダッシュボード、ハンドルが触れないほど熱くなる。さらに紫外線による内[…]
2代目ローレルは、ケンメリスカイライン(4代目)とシャシーを共有する兄弟車だった 2代目のローレルは1972年の4月に発売されました。この頃のローレルの日産内の立ち位置は“高級GT”といった感じで、ス[…]
最新の投稿記事(全体)
バッテリートラブルは夏場でも多く発生する バッテリートラブルって、寒い冬場に起きるものだと思っているユーザーが多いのではないだろうか。だが、実はエアコンなどをフル稼働させる夏場のほうがバッテリーを酷使[…]
夏の猛暑も怖くない、ロール式サンシェードが作る快適空間 夏のドライブで誰もが感じる悩みは、車内の暑さだ。炎天下に駐車すれば、シートやダッシュボード、ハンドルが触れないほど熱くなる。さらに紫外線による内[…]
暗所の映像も鮮明に記録。2つのカメラにSTARVIS技術搭載センサーを採用 ドライブレコーダーのトップブランド、コムテックが新たにリリースした新機種、ZDR-850Rは、前後2つのカメラで全方位を記録[…]
座るだけでクールダウン 夏のドライブが快適になる最新カーシート 夏の車内は、ただでさえ暑い。長時間の運転や渋滞に巻き込まれたとき、背中やお尻の蒸れが不快感を倍増させる。そんな夏の悩みを一気に解消するの[…]
大阪の商人らしい、「商いのうまさ」で誕生したコンパーノ コンパーノは、ダイハツが戦前から築き上げてきた商用車メーカーとしての地位から、乗用車市場へと本格的に参入する転機となった記念すべきシリーズモデル[…]
- 1
- 2